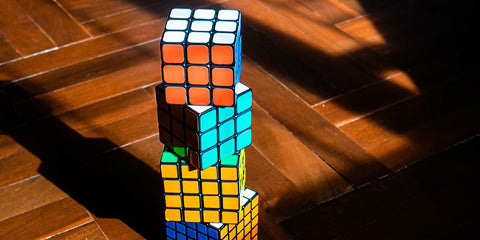
Saw Filing 101: Guide to benching wide bandsaws
By Paul Smith, is a saw filing consultant and founder of Smith Sawmill Service, now part of BID Group. You can reach him at PaulSmith@bidgroup.ca
January/February 2024 edition
Benching a band is a lot like solving a Rubik’s cube: every action must be performed correctly without adversely impacting a previous step. Photo: wachiwit / Adobe Stock
Before embarking on the journey of benching bandsaws, it’s essential to gather the right tools and expertise. This guide outlines the essential elements to get you started.
Tools needed:
- Bench with anvils and stretcher roller to accommodate the size and width of bandsaw to be benched
- Straight edges and tension gauges to properly fit the band
- Correct size, weight, and style of hammer(s) for different applications
- Back gauge
- Experienced sawfiler and apprentice, if available
- Clean: Before anything, make sure the band is clean with no rust, dust or resin all the way around on both sides.
Inspect: Load the cleaned band onto the bench. Most filers will find the butt weld and start inspecting from there. Inspect all around for any cracks, bent or broken teeth, any damage, or imperfections. If any of these are found, refer to your experienced sawfiler for the mill’s safety protocols and how to proceed. If the band checks out, move to next step.
Level: Again, starting at the butt weld, use the correct length straight edge to check for flatness. The straight edge should be long enough to reach from back of band to gullet. One should have a shorter straight edge about half the length of first one to hone in on smaller knots and lumps. Sections of the band should be looked at as the bandsaw is pulled through. The section to be worked should be no longer than the anvil and the band should lay flat on anvil without pressure. As you work the straight edges down the bandsaw you will knock the high places or bumps down with correct hammer.
Remember that a bandsaw should never be hammered where it is not needed. The object is for the bandsaw to be flat with the straight edge. If the straight edge shows a dip or valley, then it will have to be pushed through from other side.
A good rule is that if you can’t rock the straight edge on the bandsaw, then do not hit it with the hammer. Therefore, if you can’t rock it don’t knock it.
After completely going around the band, then do the other side. This can be accomplished by performing the same technique on the bottom anvil, if present. If there isn’t a bottom anvil, the bandsaw must be taken off the bench and inverted. After inverting, put the bandsaw back onto the bench and continue. This should be repeated from side to side until the bandsaw is flat. Auto levelers can be used to make this job easier, but most of the time, an experienced filer can do a better job.
Tensioning: Again, it would be good practice to start at the butt weld. For this step use the tension gauge, ground to the correct specifications for the band; and utilize the stretcher roller. Start by putting the tension gauge directly down across the width of the bandsaw without leaning the gauge either way.
In other words, the gauge should be 90 degrees from bandsaw. When using the correct gauge, the bandsaw can be picked up about three feet behind where it is being checked and the gauge should fit the bandsaw, showing little or no light under the gauge. Too much light means too much tension. If the gauge doesn’t fit the band or it isn’t flat, it does not have enough tension. Some benches will have an air-operated cylinder to lift the bandsaw. Just as with the leveling, do not roll where it isn’t needed or it can make the band worse. Tension should be even and the same all the way around. This process also must be performed from side to side until both sides are the same and properly tensioned. An automated tensioning bench set up and maintained properly can make this job much easier.
Tire lines: As with every aspect of the bandsaw, correct tire lines are important. The tire lines determine where the bandsaw will run on the wheels.
The front tire line enables the bandsaw to cut a straight line without wash boarding. Normally the front tire line on hardwood is run closer to the gullet than in pine lumber. The further back from the gullet the tire line, the less likely one should experience gullet cracking. Tire lines are moved by pushing them one way or another with the stretcher roller. Remember that when moving tire lines, it is highly likely that tension can be added or taken away.
Checking and rolling correct back: Although this may be one of the last checks in repairing bandsaws, it may well be the most important. The back of the bandsaw needs to be uniformly longer than the cutting edge for the entire length of the blade. When correct, it will keep the bandsaw from running back off the wheels while keeping the front edge taut. The cutting edge must be shorter than the back as the back follows the cutting edge and should just glide without issues behind the cut. As with all aspects and processes to repair bandsaws, this may be the most important when it comes to safety. If done incorrectly, leaving the back longer than the front can allow the band to come off the wheels, endangering operators and equipment.
Every series of actions in benching a bandsaw will affect different actions already performed in separate ways. For example, adding tension may cause flatness, tire lines, and back to move in a way that will no longer allow the bandsaw to operate and run satisfactorily. An uncomplicated way to look at benching a band is a lot like solving a Rubik’s cube. Every action mentioned above must be performed correctly without adversely impacting a previous step. The object is to end up with all of the actions showing the true colours of the experienced filer at work. As an influencer, I suggest an experienced sawfiler perform the benching of the mill’s bandsaws. Of course, using an apprentice with an experienced sawfiler is even better. Equipping the filing room with a fully automatic benching machine is a way to increase output, enhance safety, and to consistently put out quality bands. Adding automation doesn’t mean eliminating the experienced filer, it means that person isn’t burnt out by repetitive tasks and is freed up to work with and train apprentice filers.